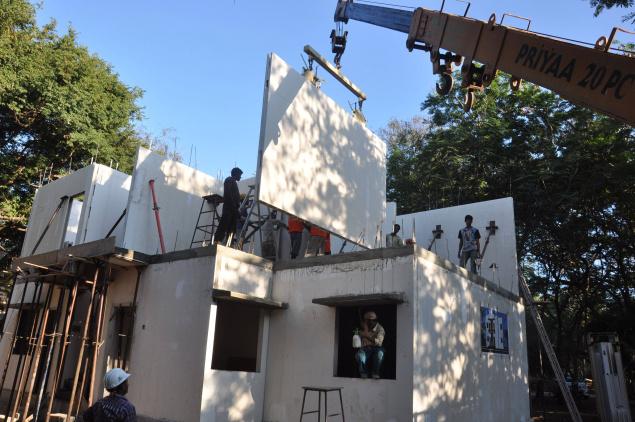
Panels made of glass fibre reinforced gypsum can replace brick walls and RCC slabs, and are resistant to quakes.
Can panels made of gypsum reinforced with glass fibre be used as load-bearing walls replacing brick in a multi-storied building? Can they also be used as floor/roof in place of reinforced cement concrete (RCC) slab? The simple answer is, yes.
A few years ago, Rapidwall Building Systems, Australia, developed a technology to make gypsum strong and water-resistant enough to be used as load-bearing walls. This is by calcining process where glass fibre is combined with gypsum plaster to produce glass fibre reinforced gypsum (GFRG) panels. Now, researchers at IIT Madras have gone a step further.
They have developed a technology to make GFRG panels to be also used as floor/roof, thus eliminating the use of RCC slabs. An eight-storied building, for instance, can be built using the panels as load-bearing walls, floors/roofs and staircases.
They also collaborated in the indigenous development of an excellent water-proofing material. Water-proofing is essential for prolonged durability of the GFRG panels, especially in the case of roofs and toilets.
A demonstration building — ground plus first floor — is being built inside the IIT-M campus. The building, with electrical and sanitary fittings, will be ready on April 8 — just 29 days of construction after the foundation was completed. “It will be ready for occupation when it is completed,” said Prof. Devdas Menon, Department of Civil Engineering, IIT Madras.
The building will have four units — two with a carpet area of 269 sq.ft are for the economically weaker section, and another two, with a carpet area of 497 sq.ft, are for the low-income group (LIG).
A few years ago, a couple of buildings were constructed at the GFRG panel manufacturing plants at RCF in Mumbai and FACT Cochin, and one at Visakhapatnam using the IIT technology. “Those were pilot projects,” said Prof. Menon. “This is a demonstration that the material can be used for cost-effective, mass-scale and quickly buildable housing, with improved water-proofing.”
What makes the rapid construction possible is that the panels are prefabricated and cut to desired sizes based on room sizes with openings for doors and windows.
A panel has two skins of 15 mm thickness that are interconnected at regular intervals (25 cm). The cavities formed by these interconnections are used for several purposes — filling with concrete, and laying electrical conduits and plumbing pipes.
In Australia, the Rapidwall technology has been used for constructing several 2-3 storied buildings. Since the walls act as load-bearing structures, every cavity in the panel is filled with concrete. They use conventional RCC solid slabs for the roof/floor.
“We recommend the use of two steel bars instead of one and filling all cavities with concrete in the lower floors in the case of a high-rise building,” said Prof. A. Meher Prasad of Civil Engineering Department, IIT, Madras. The number of concrete-filled cavities and steel bars keeps reducing from the ground to the topmost floor. The topmost floor will need very few concrete-filled cavities.
A reduction in amount of concrete used in turn reduces the total weight of the building. The ripple effect is the reduction in the foundation cost. The demonstration building at IIT Madras is about 25 per cent cheaper than conventional ones. “There will be greater savings when used for mass-construction,” Prof. Menon stressed. Aside from the savings and speed of construction, the buildings are subjected to lesser earthquake forces. This is because of their lighter weight.
For the floor/roof, the panels are placed over the vertical wall panels and the top skin of every third cavity is cut open. Steel reinforcement is placed in these cut cavities before being filled with concrete. The concrete-filled cavities tend to behave as hidden beams. The panel is then covered with a 5-cm thick concrete topping.
Since the panels have a smooth finish, the need to plaster them (as in the case of brick walls) does not arise. The total weight of the building (dead weight) is reduced substantially
According to the IIT researchers, tests conducted have shown that GFRG panels reinforced with concrete are also capable of resisting lateral loads caused by earthquakes. During an earthquake or strong wind, buildings tend to sway and the walls are subjected to enormous loads exerted laterally.
The Building Material & Technology Promotion Council (BMTPC) has approved GFRG for construction in India.
source: http://www.thehindu.com / The Hindu / Home> S & T > Technology / by R Prasad / April 03rd, 2013
I need to construct 800Sq.Ft house at lower cost , please some one help me to guide to go for GFRG concrete wall.
My contact No : 9789039305